Aluminum extrusion
Aluminum extrusion is a mechanical process that involves converting large, solid blocks of various alloys into long profiles of specific cross-section. The raw material is heated and piston-pressed via a hardened-steel die, with a centrally located holed giving the profile its shape.
After the process, the product is stretched, cut and cooled, which are required to obtain the desired strength and stiffness of the final product.
Exlabesa currently owns 30 extrusion presses with a pressure force ranging from 13 MN to 85 MN. Such capabilities position us at the global forefront of the industry and enable satisfying the demand for extruded aluminum in all its applications, allowing us to manufacture profiles fully tailored to the needs of the clients and every project. In addition, our highly flexible and dynamic manufacturing system has led to achieve a production capacity of 238,000 tonnes per year.
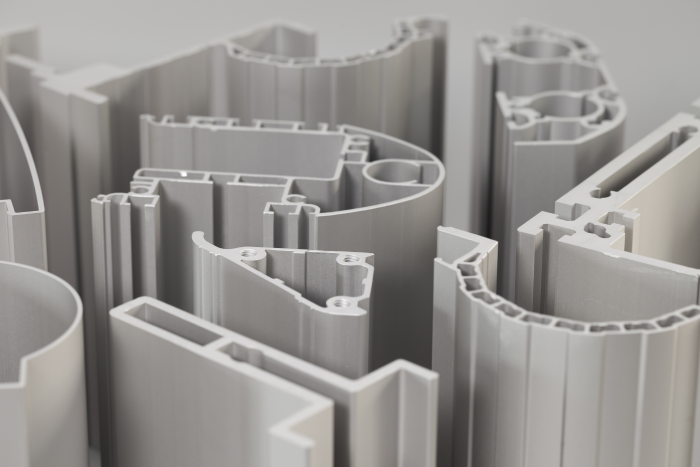
30 extrusion presses with a pressure force ranging from 13 MN to 85 MN.
Alloys: 6005, 6005A 6060, 6061, 6063, 6101, 6463, 6705.
Maximum extruded profile length: 28 000 mm.
Annual manufacturing capacity: 238 000 Tm.
Diameter: from 8 mm to a maximum of 700 mm.
Standardized profiles.
Maximum profile weight: up to 120 kg/m.